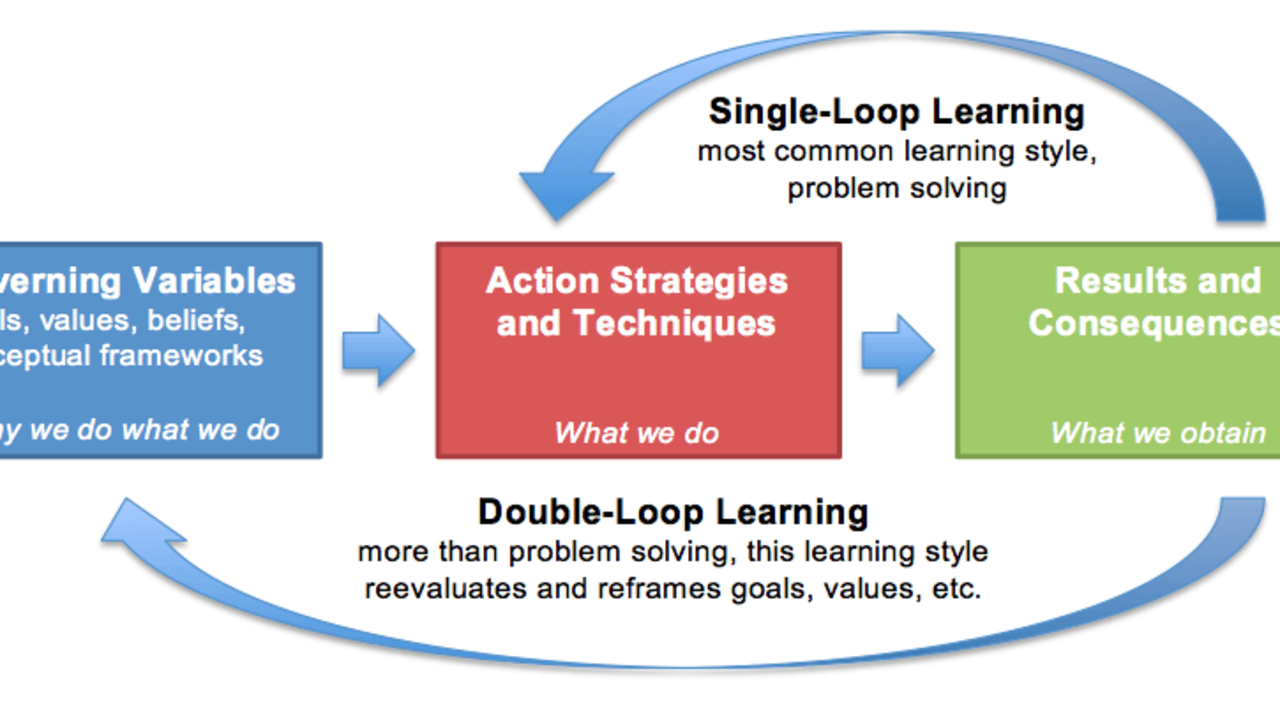
Technical Solution, New Process/Rule or Behavioural Change? - LFI Seminars Part 1
Dec 22, 2015I recently attended a seminar in London where the aims of the sessions were to understand how different organisations and individuals learned from incidents. Those attending included legal professionals, Health and Safety experts, academics covering safety, behaviour and learning and operators / industry including construction, maritime and oil & gas. I believe I was the only person representing any recreational-type activity which lead to an interesting view of how safety is 'managed'. I will cover a number of different themes from these seminars but I will start with the theme of improving safety by understanding behaviours...
If we look at incident and accident reports from across the different domains, a key theme rises to the top - humans make mistakes and errors no matter how much has been done to technically engineer out the problem. Notwithstanding this ‘root cause’, it is recognised that ‘human error’ is a poor attribution when it comes to incident investigation and as a consequence, many individuals and organisations spend considerable time and effort improving the engineering solution to the problem (technical) and once those have been incorporated, they then start to look at processes (either rules or training) to reduce the risk further. However, the point that was made in one of the presentations, is that the key area that organisations should be looking to modify are behaviours and assumptions as these underpin everything.
Situation: Diver picks up a cylinder with nitrox in it from a dive centre he visits regularly. He knows the staff well and they have always given him what he wants in terms of gas. However, on this occasion, the staff member has forgotten to top off the O2 with air. In addition, the diver is in a hurry as he has another meeting to go to and is already running late. He does not have an analyser at home.
- Assumption: The diver trusts the staff to fill and mix the gas correctly. The mixes have always been within 1% when he has analysed the gas (but this hasn’t always happened).
- Behaviour: The diver picks up the cylinder, pays and leaves the shop without analysing the gas. He dives the cylinder and there might be a problem - this might be fatality. If there isn’t a problem, there is a potential that this starts an incorrect behaviour because it ‘was ok the last time’. This reinforces the incorrect assumption that the filling station provide correct gases. Unfortunately there are a multitude of incidents where gas has not been analysed correctly (or at all) and a fatality has occurred as a consequence.

Gareth Lock is the owner of The Human Diver, a niche company focused on educating and developing divers, instructors and related teams to be high-performing. If you'd like to deepen your diving experience, consider taking the online introduction course which will change your attitude towards diving because safety is your perception, visit the website.
Want to learn more about this article or have questions? Contact us.